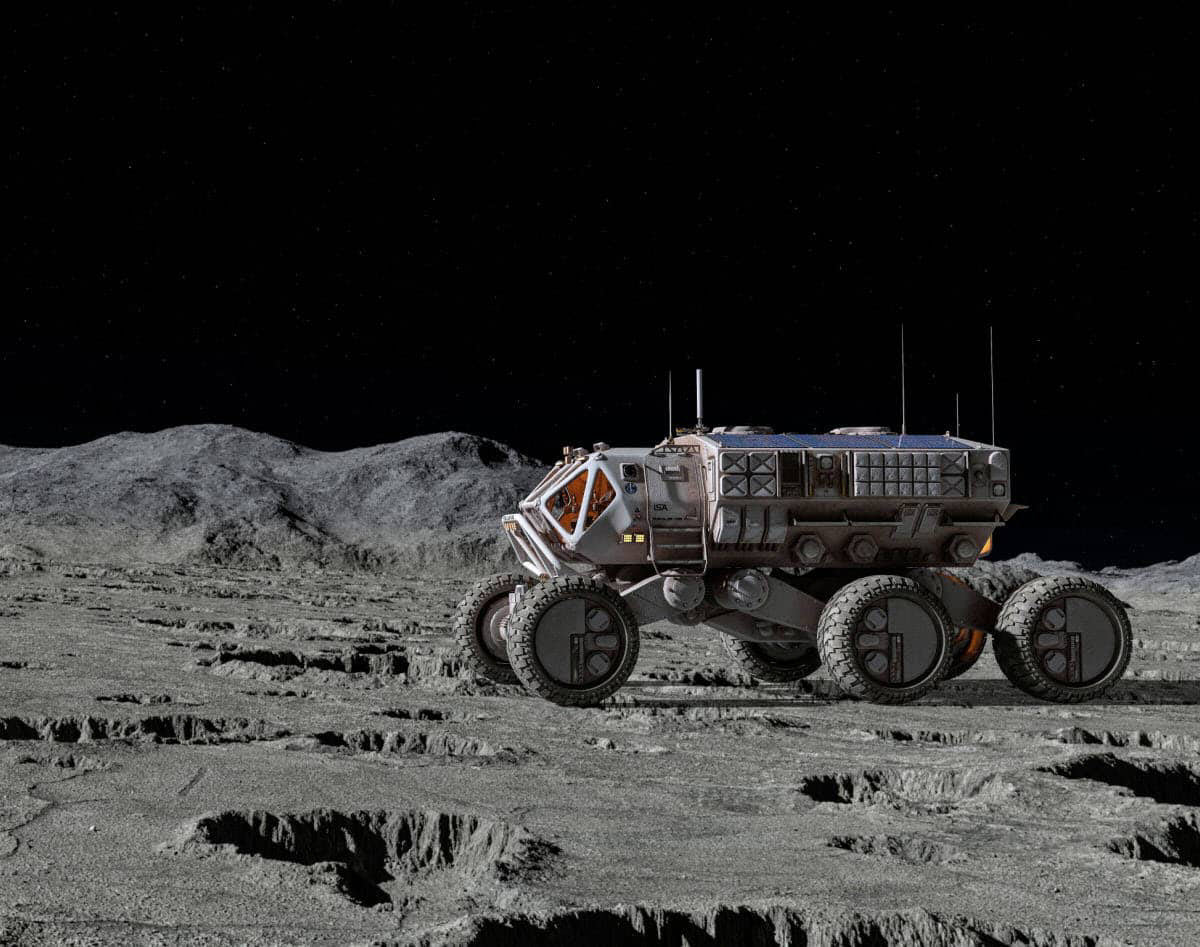
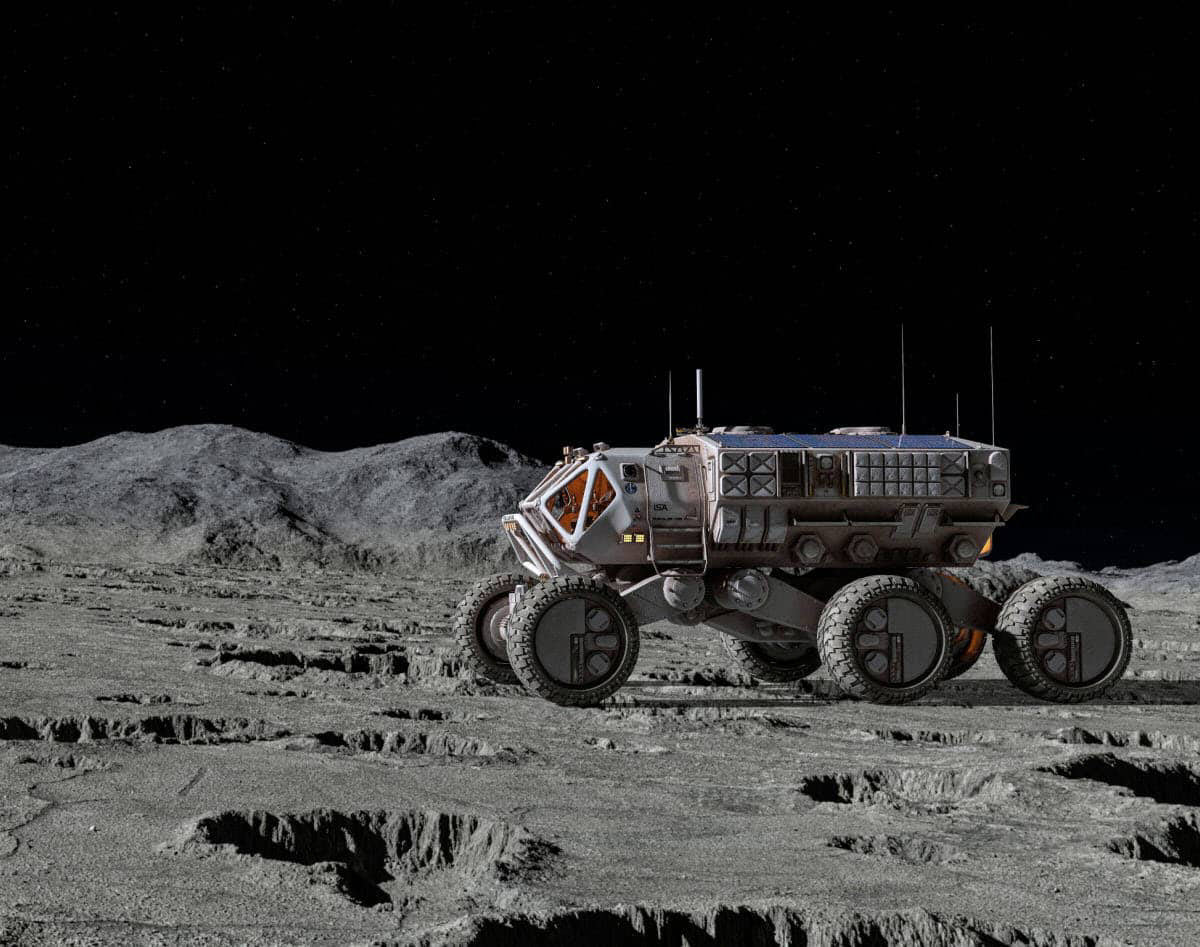
Intergalactic recently announced it was issued a patent by the U.S. Patent and Trademark Office for the company's proprietary microtube heat exchanger technology. U.S. Patent 11,519,670 is wide-ranging and covers general design, manufacturing process, and a broad array of applications of microtube heat exchangers in defense aerospace, civil aviation, and space contexts.
The patent, which has been patent-pending for the past two years but is now fully issued, protects “laser-welded microtube heat exchangers in aerospace environmental control systems,” which applies to any aircraft or spacecraft thermal management application. This includes, but is not limited to, electronics cooling or heating, aircraft or spacecraft habitat thermal conditioning, temperature regulation of mechanical systems such as engines or transmissions, bleed air cooling, and similar applications in the defense aerospace, civil aviation, and space sectors.
“We’re proud to have pioneered and perfected microtube technology for airborne and space applications,” says Intergalactic CTO Nick Kaiser, who is listed as an inventor on the patent. “Our microtube technology and manufacturing processes are critical to reducing the size and weight of high-performing thermal management systems required to deal with rising heat loads. We’re grateful to have our work on this innovation recognized with a U.S. patent.”
Covered in depth in a previous TechBuzz article last April, Intergalactic, based in St. George, has developed microtube heat exchangers in air and space contexts. The patent—the first for the company—covers the following:
- Use of all fluids in microtube heat exchangers, including air, liquid coolants, oil, refrigerants, and more.
- Intergalactic’s proprietary construction style, which consists of end plates with holes, multiple microtubes between the plates, all laser welded together.
- A broad range of applications, including various fluid types and flows (including liquid, ram air, and more), mid-plates for flow direction control, tube reinforcement for protection against foreign object debris and damage, and various tube bank geometries (e.g. square, curve, arc, U-shape, and others).
- Various tube arrays and spacing patterns.
- Specific coverage of ram air duct installations which are common in next-generation defense aerospace applications.
Intergalactic’s microtube heat exchanger is a step change innovation, applying a novel laser welding process to improve robustness while unlocking significant size and weight savings without compromising performance and reliability, even in the most demanding environments and conditions such as those found in MIL-STD-810 and DO-160. As Tony Ho, Intergalactic’s Head of Systems Engineering, wrote in SAE Mobility Engineering:
"Intergalactic routinely observes that microtube heat exchangers have shown 3x to 4x the capacity of a conventional plate fin heat exchanger for the same core volume. Alternatively, if one is more sensitive to weight or volume, one could shrink down the size of a microtube heat exchanger to maintain the same performance as a conventional heat exchanger, but significantly reduce weight and installation footprint. In real-world aerospace applications, Intergalactic has seen 50%-80% reduction in weight and/or volume for microtube heat exchangers compared to conventional heat exchanger technology."
Microtube heat exchange technology is made up of thin metal tubes "that are are analogous to a medical syringe," shared Brad Plothow, the company's Chief Growth Officer, with TechBuzz. "The tubes are made of stainless steel and have very small wall thickness—a fraction of the size of a human hair in some cases—depending on what we're trying to develop. We're stacking thousands of them in an array, putting end plates on both sides, and welding them together using a precise, proprietary laser welding process."
Plowthow explained that the robust welding process is critical to ensure everything stays together in harsh space environments or critical aviation applications such as weapon systems components on fighter jets.
Intergalactic’s microtube heat exchanger has proven durable in adverse conditions. It is rated TRL-8 (a scale NASA uses to assess the maturity of a given technology). It has been field tested at Mach 1, 27 G’s of force, and 14,000 PSI. It is central to all Intergalactic’s branded, off-the-shelf thermal management systems.
Intergalactic’s microtube heat exchanger won first place at the 2022 Utah Innovation Awards in the advanced manufacturing, construction, and design category. It’s available in virtually any form factor and branded as Boreas3 for defense and civil aerospace applications and BoreasX for space applications. This patent marks the first patent for the company, which was founded in 2016.
As a technology innovator in the aerospace—a sector difficult to break into for startups and one known for long product cycles and technology development arcs—Intergalactic has a long-term vision for its role in the aerospace industry.
"I come from the world of venture backed software companies where things move much more quickly," says Plothow. "But once you start to see these technologies compound, you own that piece of the market for decades. And that's what we're trying to do, to reinvent the technology standard for thermal management. We see our thermal management technology standard being used in other applications: innovations such as laser weapons on military aircraft, lunar rovers that will enable permanent human occupation on the moon—astronauts can treat the rover like an RV and sleep in it. All these things require much different ways of thinking about the temperature concerns. And that's really why we exist, to reinvent the technology standard that enables those upstream innovations. This patent is an important first step, but there will be many more that layers on top of this."